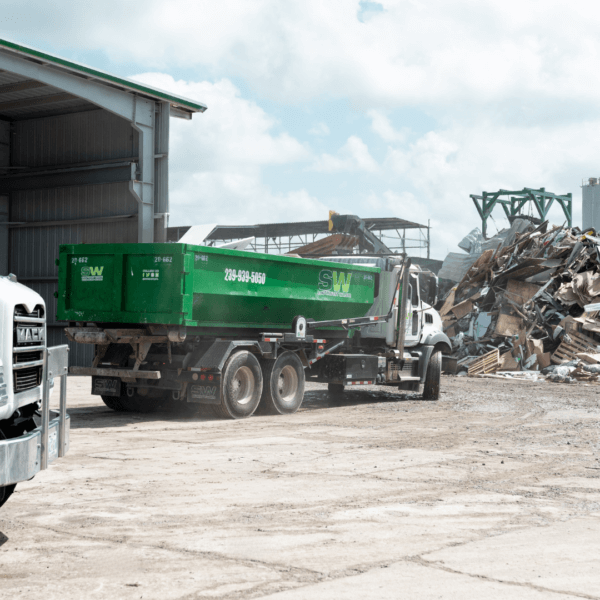
Receiving in the Procurement Process
Hayley Campbell
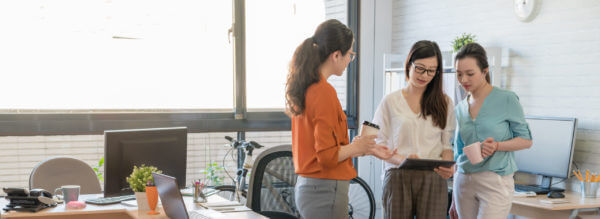
Procurement
Blog
A behind-the-scenes look at the receipt of goods process
A milestone event in the procurement process occurs when the items you’ve ordered arrive in your warehouse. Did you get the right product? Is it of the quality you expect? Was the correct quantity delivered? Simple questions, perhaps, but how your company systematically goes about answering them can have major impacts on efficiency, productivity, and ultimately profitability. In our continuing series covering the basic steps in the procurement cycle, we take a behind-the-scenes look at the receipt of goods process — what’s involved and why it matters.
Where does it begin and end?
The receipt of goods process matches the goods that a company receives with the purchase order you issued to a vendor, verifying that the goods received are what was ordered and that they are undamaged. The process starts with the purchase order (PO) and ends with the successful handoff of the goods to the requester and the invoice to the payables department. At its most basic, the receipt of goods process consists of three steps:
- Inspecting the goods
- Comparing to the PO
- Updating the quantity and posting the receipt
Often, the vendor invoice is received after the goods have been received, in which case there’s an additional step of matching the invoice with the receiving documents. We’ll cover invoice matching in more detail in an upcoming post.
Inspecting the goods: quality and quantity count
When a shipment arrives, it’s important to confirm that you received the right goods in the right quantity.
How thoroughly you verify the quantities received will likely vary by how many packages are involved, and how important the contents are. If there are many packages, and there are many items in each package, complete counts would be a very time-consuming process. In those cases, it may be better to use sampling to establish the quantity received. A sampling of a few of the packages can be done by weight, physical dimensions, or an individual count — whichever method makes the most sense for a particular product.
Depending upon the importance of the product and its intended use, quality checks may or may not take place during the receiving process. In some industries, food production, for example, products may be received into a quarantined state, to undergo stringent quality and composition testing. Typically, though, a quality check made during the receiving process is made to catch damage that occurred during shipping.
Comparing to the PO: paying only for what you get
Naturally, you’ll only want to pay vendors for the correct merchandise received in the proper quantity and of acceptable quality at a price agreed upon, so you’ll need to compare receiving documents against the PO.
If the shipment arrives without a vendor invoice, this step is covered during the inspection process. However, it’s important for your accounts payable department to have documentation supporting the successful receipt before payment is approved. Documents including the purchase order, receiving report, packing slip, and vendor’s invoice can be filed together (preferably in electronic format) and attached during the receipt process so that they are readily available when the invoice is received, and bills are being paid.
Recording the receipt: tools to get it right
Once you’ve inspected the incoming goods and confirmed that the items and quantities agree with what was ordered on the PO, you’ll want to record the receipt against the PO formally. Using electronic procurement (eProcurement) software to record and track the receipt of goods process brings efficiency and helps build best practices in several ways.
Using eProcurment software eliminates the need for staff to rekey item information; they can simply confirm the quantities received to update the PO. EProcurement solutions can also perform automatic 2- or 3-way matching of the vendor invoice against the PO and receiving documents. Once an item is recorded as received in your eProcurement software, it can be included in your inventory availability count, providing accurate information to the customer service, purchasing, and warehouse personnel. The value of the received goods or services is recorded in your accounting system, awaiting reconciliation when the invoice is received. In addition, eProcurement software can automate workflows, ensuring proper procedures are followed, and providing alerts and notifications to keep the process moving and notifying stakeholders of important events and developments in the process.
The benefits eProcurement software brings to the receipt process can’t be understated, so we’ve summarized them for you here:
- Minimize risk of paying for goods you didn’t order, or overpaying for those you did order
- Keep inventory stock levels accurate and up to date
- Track the value of goods and services that have been received but not yet invoiced
- Speed up, streamline, and ensure greater accuracy of the payables process
- Communicate to the purchasing team/buyers that a purchase order line is closed
- Automatically alert the requester that items have arrived (or have not arrived by due date)
Interested in improving your company’s procurement cycle? See PairSoft in action here.
What's stopping your procurement process?
Talk to an expert today to uncover how your team’s procurement stacks up against the top performers in your sector.
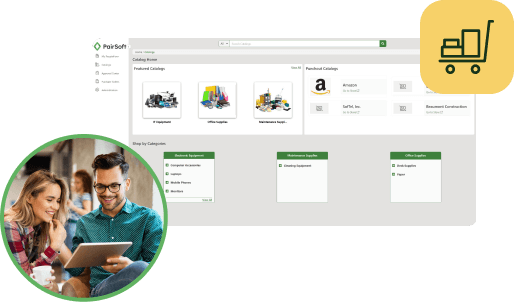
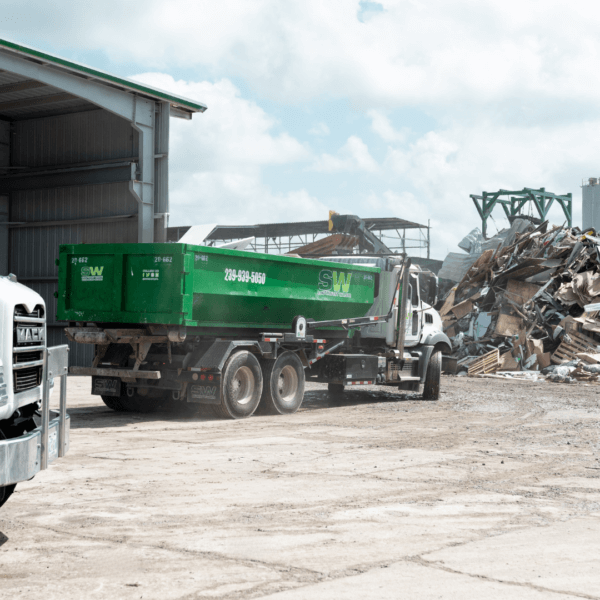
Simple solutions. Powerful results. Seamlessly integrated.
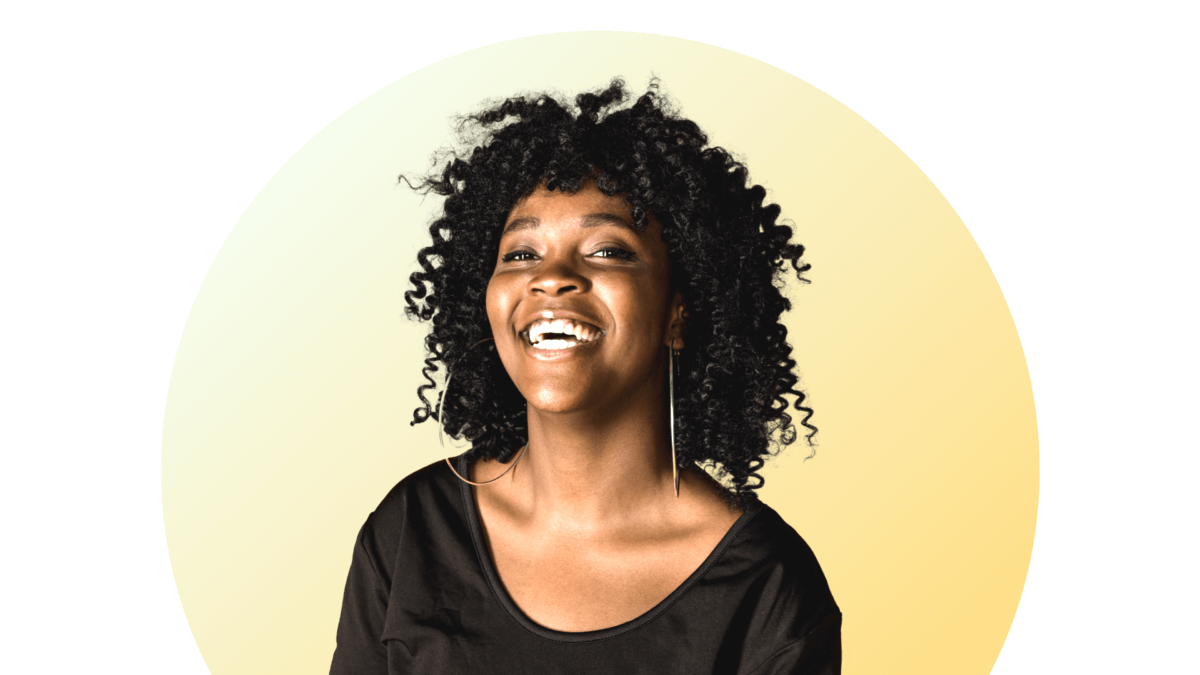